Airbus is progressing on his journey to put in commercial service a zero emission Aircraft by 2035. In the last few days we have revealed our development on a hydrogen-powered fuel cell engine. We consider this propulsion system as one of the potential solutions to reach our ambition. We will continue on our trajectory, next key step will be to start ground and flight testing this fuel cell engine architecture onboard our ZEROe demonstrator aircraft towards the middle of the decade.
In order to support this very challenging development, fully inline with our company’s purpose, “pioneering sustainable aerospace for a better and united world“, digitalization will be a key enabler. That’s why back in 2019 we have launched our main digital transformation program DDMS, one of the key pillars is on modelling and simulation and MBSE. These will permit us to de risk upfront all those new technologies via complex simulations in a very integrated manner across all the different disciplines and engineering teams. This new challenge is in fact highly multidisciplinary and will require to find a design global optimum instead of a typical set of local ones.
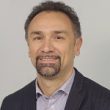
Marco Ferrogalini
Vice President , Head of Modelling and Simulations (MBSE)
Airbus
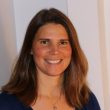
Sandrine Rolland
ZeroE A/C Architect for V&V strategy
Airbus
Starting from the main challenges and stakes that faces Systems Engineering in Aeronautics, Defence and Space, today and from analysis of technical failures (abandoned programs) or economic failures (cost overruns and quasi-systematic delays in certain domains), observed in many major programs in the aeronautics, space and defence perimeters, the GIFAS WG has identified 10 major recommendations among 80 more detailed ones.
In a second phase, a joint working group AFIS-GIFAS has been settled to address recommendation proposing a method to implement a collaborative approach at Extended Enterprise level generating more value for company’s stakeholders based on their respective ecosystems. The main outcome is the creation of a generic process framework model based on on international SE standards supported by the knowledge and experience of participants.
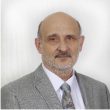
Christophe Ducamp
Systems Engineering Senior Expert Design for Lifecycle,
Aeronautic Defence Space,
Airbus
Model-based system engineering (MBSE) can effectively reduce the time and cost of complex equipment development and improve the quality and development efficiency. Many domestic and foreign aerospace enterprises are trying to implement MBSE. Still, the effect varies widely due to the lack of implementation guidance, and lots of enterprises stay at the stage of using the MBSE modelling tool replacing Microsoft Visio. To solve this problem, this paper analyzes the three stages of system modelling capability. It improves the typical MBSE implementation process based on Deming Cycle and proposes an MBSE implementation framework based on multiple modelling capability stages. The process framework emphasizes implementing MBSE step by step, providing an efficient reference for complex equipment R&D enterprises to transform from document-based SE to MBSE.
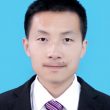
Yuqiang Guo
System Engineer,
China Helicopter Research and Development Institute
The railways have traditionally approached systems architecture following a national – even regional – technical approach, leading to a heterogeneous picture at European level. National markets for rail infrastructure and vehicles continue to exist in a way that has been overcome in other modes of transport or sectors. The problem with this is that innovations and changes to the system are very difficult and costly to achieve. Ultimately this undermines the performance and competitiveness of rail, including with its ability to easily interface with other complementary non-rail systems.
The purpose of the System Pillar is to improve the European railway system to offer better services for the European citizen, passengers and freight through, inter alia:
• Cost efficiency for integration
• Migration and deployment,
• Cost efficiency for maintenance and evolution of the system
• Quicker roll-out of innovations
• Market accessibility (for equipment and service provision)
• Increase overall performance and agility of the railway including time, reliability and safety towards the customer through faster deployment of key new technologies
• Improved train service delivery across the European Union
• Facilitate rail as integral part of the mobility services across the European Union
• Manage diverse rail legacy, bringing interoperability and ease the migration
• Sound, qualified and reliable supply chain.
As set out in the SBA , EU-RAIL will develop in its System Pillar a system view that reflects the needs of the rail operating community, Infrastructure Managers, rail manufacturing industry, Member States and other rail private and public stakeholders, including bodies representing customers, such as passengers, freight forwarders, and staff, as well as and relevant actors outside the traditional rail sector. This will be reflected in the System Pillar governance, through the System Pillar Steering Group.
The ‘system view’ shall encompass, as defined in Article 86 of the Single Basic Act:
a) the development of the operational concept and system architecture, including the definition of the services, functional blocks, and interfaces, which form the basis of rail system operations;
b) the development of associated specifications including interfaces, functional requirement specifications and system requirement specifications to feed into Technical Specifications for Interoperability (TSI) established pursuant to Directive (EU) 2016/797 of the European Parliament and of the Council or standardisation processes to lead to higher levels of digitalisation and automation;
c) ensuring the system is maintained, error-corrected and able to adapt over time and ensure migration considerations from current architectures;
d) ensuring that the necessary interfaces with other modes, as well as with metro and trams or light rail systems, are assessed and demonstrated, in particular for freight and passenger flows.
A successful System Pillar will:
• Make the most efficient use of scarce resources (EU and Member States, rail sector, both financial and human capital), coordinating and consolidating initiatives under one umbrella.
• Align public and private EU Research and Innovation initiatives with a long-term operational concept and system architecture, supporting interoperability, and to the legal and regulatory framework, to ensure a strategic plan for an overall harmonised approach.
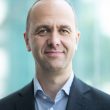
Ian Conlon
Head of Unit, System Pillar
Europe’s Rail Joint Undertaking
In the frame of Digital Transformation of the French Industry Sectors, the ATLAS program supports assessment and adoption of standards. ATLAS is a follow up for a successful initiative, which implemented digital platforms for Aeronautics and Building Industries. In this scope, standards for interoperability and digital continuity are main concerns. Standards have the potential to strengthen opportunities, improve productivity, and encourage technology adoption, while reducing risk, improving safety, and complementing policy and legislation. This paper focuses on the Systems Engineering (SE) domain of ATLAS where the strategy is jointly defined with the French chapter of INCOSE (AFIS). This strategy is organized along five orientations and is refined in the different project typologies, which serve the various maturity of companies and industrials sectors against their digital transformation and their SE adoption.
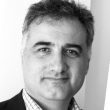
Pascal Hubert
Program Director,
AFNeT Services
Based on the analysis of the development trend of avionics systems, this paper presents a concept of advanced avionics architecture oriented towards system integration. By using open interface standard and service-oriented design method to decouple the application and resources of traditional avionics system, the support of avionics system to the requirement of equipment informationization, networking and systematization is realized. The characteristics of advanced avionics architecture, such as hierarchical distribution and flexible grouping, as well as the application support for the rapid integration of air combat system are introduced. Finally, the core technologies related to the architecture design of advanced avionics systems, such as model-based complex system design, open avionics system architecture design, and advanced avionics system architecture specification system definition are analyzed.
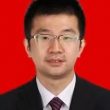
Qing Zhou
Institute Chief,
China National Aeronautical Radio Electronics Research Institute
This paper presents a study on the application of data-driven and symbolic artificial intelligence to the architecting, design and operation of Product-Service Systems (PSS). The study provides a vision on how the power of AI techniques can be unleashed to enable organizations to offer innovative functionalities such as performance-based contracts, PSS architecting and smart maintenance through a better use of data and business knowledge.
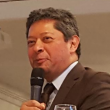
Hugo Guillermo Chalé Gongora
Product Line Engineering Director,
Thales
Modelling and Simulation enable the virtualization of the system design and its environment, from the component level up to the system and higher. It is this higher level where we usually hear about digital engineering. The expected benefits of digital engineering include better-informed decision-making, enhanced communication, and increased confidence in the system design, aiming at an overall more efficient engineering process.
Acknowledging that systems are increasingly complex as technology grows, and following the path of digital engineering, new challenges arise such as defining requirements while integrating lower-level constraints or domain specificities to comply with the operational mission.
Enabling Model-Based System and Software Engineering in a unified ecosystem like MATLAB® and Simulink®, offers a common ground for communication and integration. It offers the capability to establish and check the system requirements consistency and traceability, ensure the functional behaviour, or run parametric analyses from different levels of perspective.
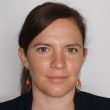
Alexandra Beaudouin
EMEA Aerospace and Defense Industry Manager,
MathWorks
In order to combat climate change and to reduce greenhouse gas emissions, more and more clean electricity will be used. But for hard to decarbonize sectors (heavy duty mobility, heavy industry for instance) and to provide flexibility to the power system, the development of H2 technologies is essential. Based initially on local ecosystems and clusters, a worldwide market for clean hydrogen and its derivatives (ammonia, methanol, SAF,..) will develop progressively and will create a new geopolitics of energy.
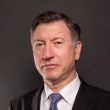
Philippe Boucly
President,
France Hydrogène
Simulation has been a key factor of the massive adoption by most industries of Model-Based Systems Engineering (MBSE) and Model-Based Design (MBD) tools. Meanwhile, practical Requirements Engineering tools have not significantly evolved beyond the lifecycle management of document-centric specifications, leaving requirements aside from model-based simulation tools. Requirements-In-the-Loop (RIL) simulation has been proposed to extend MBSE and MBD frameworks with textual yet formal and executable requirements models. RIL simulation allows generating discrete-time systems behaviors based on the requirements semantics as well as to check that other behavioral models like state machines comply with systems requirements. This paper introduces the principles of Requirements-In-the-Loop simulation and illustrates its benefits on the Landing Gears case study. Especially, this work demonstrates the ability of the Stimulus tool to detect incorrect, missing or conflicting requirements of a realistic system and to test its model-based specification against requirements.
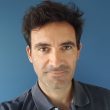
Fabien Gaucher
CATIA Systems Requirements R&D Director,
Dassault Systèmes
Model-Based Systems Engineering (MBSE) is increasingly adopted across the aerospace industry for the development of complex systems. As specified by aerospace standards SAE ARP4754A and ARP4761, the Functional Hazard Assessment (FHA) is a mandatory safety assessment process performed at the early phases of development. It examines aircraft and system level functions to identify and classify failure conditions, hence supporting the derivation of safety objectives and requirements. However, the link between MBSE and safety assessment still needs further improvement, particularly regarding failure conditions and FHAs. This paper introduces a UML profile extension that enables the modelling of failure conditions and generation of FHAs which can be used alongside any UML-based systems modelling profile, such as OMG SysML. This profile enables preliminary safety data to be modelled and analysed during operational analysis, allowing safety considerations to be integrated earlier in the development process and supporting a better flow down of safety requirements.
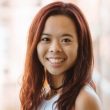
Kimberly Lai
Teaching Assistant,
University of Toronto
Maritime autonomous surface ships (MASS) have been proposed to significantly transform the maritime industry. While research and development are underway worldwide, fully autonomous ships have yet to be commercialized, hindered by technical, economic, and legal constraints. Ship builders and ship owners together must weigh how to invest limited budgets and attention to adopt MASS. This research demonstrates a model and simulation to explore the interplay of decisions and actions by maritime stakeholders, including R&D investment, technology readiness of various autonomy subsystems, and learning curves in manufacturing and operation. These factors are examined across specific types of ships to bend the adoption curve, so that industrial capability and adoption of MASS are accelerated. By exploring the tradespace of combined decisions toward the introduction of MASS, roadmaps are crafted which can be tuned to particular industrial maturity, resources, and market. Simulation results for a specific ship type and market are shown.
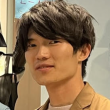
Takuya Nakashima
PhD Student,
University of Tokyo
In the frame of and ESA study, Samares Engineering and Airbus Defence and Space performed the reverse engineering of a CubeSat with MBSE. The first step consisted in translating mission and technical textual information from documentation to a model. The model was built with the Airbus MBSE framework, following a grid of five abstraction layers, from mission analysis, operational analysis, functional architecture, logical architecture, down to technical architecture. The second step consisted in completing the model by introducing functions and logical components to ensure full digital continuity between mission and technical components. The identification of the system functions was difficult, whatever the approach taken (top-down refinement or abstraction from equipments). Finally, the reverse engineering process was updated by introducing functions directly as inputs, derived from experience, and it strongly eased the process by reducing the gap between mission and technical components.
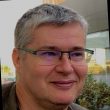
Raphael Faudou
CEO and Model-Based Systems Engineering expert,
Samares Engineering
Although practitioners greatly appreciate the importance of interface design in the system architecting process, engineering design and system engineering (EDSE) researchers have focused primarily on module selection, with interfaces only considered in terms of implementation. Consequently, interface design is overlooked when evaluating the goodness of architectural alternatives or developing modularization algorithms. However, our findings demonstrate the strong interaction between modularization and interface design, which limits the effectiveness of this traditional approach. To examine the joint impact of interface design and modularization choices, we construct a simulated model and conduct a controlled experiment. Our findings are critical for both the researchers and the practitioners of the EDSE community. We find that the relative preference among modularization alternatives greatly varies depending on interface design archetype. Moreover, the co-design of these two features create novel opportunities to navigate the cost-performance Pareto-Frontier. Thus, it is imperative to consider interface design during tradespace exploration exercises.
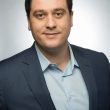
Taylan Topcu
Postdoctoral Research Scientist,
Virginia Tech
For Model-based Systems Engineering (MBSE) to reach its full potential it is important to take the step from descriptive modelling to re-using the system models for analytical purposes beyond simple model execution. This paper describes an extension of the Systems Modeling Language (SysML) for explicitly modelling flow-based analysis processes that integrates discipline-specific models. Furthermore, it provides details about the implemented supporting tool infrastructure for automatic execution of different kind of analyses in a heterogeneous tool landscape that is deployed in a cloud environment. Additionally, the paper exemplifies this approach with a small case study from the aeronautic domain.
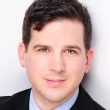
Philipp Helle
Expert Digital Technologies for MBSE,
Airbus Central R&T
Systems Engineering research findings often fail to be adopted by industry, despite using a thorough and rigorous research methodology like the Design Research Methodology (DRM). Industry as Laboratory is a research approach that improves relevance for industry by embedding parts of the research in real industry settings. A drawback is that experimenting in industry is done after extensive and time consuming analysis, leading to lost interest by the company. Further the extensive analysis phase described in the DRM can result in analysis lock-in for the researcher.
The Spiral Approach for Systems Engineering Research (SASER) introduced here increases the rate of experimenting in industry by mating the established spiral development approach with rigorous design research as defined in the DRM. This way, the company can see and adopt findings earlier, and the researcher can see the results sooner. The expectation is that not only the company remains interested, but also the researcher stays motivated and avoids the analysis lock-in. The paper presents SASER and illustrates it with a descriptive example.
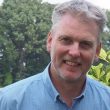
G.Maarten Bonnema
Associate Professor in Systems Engineering,
University of Twente
Design began its digital transition in the 1970s with CAD. Model-Based Systems Engineering (MBSE) would accelerate the process by profoundly modifying the structures and operations of design offices. The question therefore arises of describing what the adoption of a systemic innovation such as MBSE is and of deducing prescriptions. The difficulty is in the multidimensional nature of the adoption of the innovation. This adoption combines technical, organisational, managerial, but also individual processes that have so far been poorly defined and addressed from different approaches. In this paper, we propose a state of the art on some of them. We will focus on an objective approach to MBSE, so as to define what it is for the Systems Engineering (SE) community; then on an approach centred on the maturity of processes, since MBSE assumes a more consistent mastery of modelling than documentary SE; and finally, we will address the adoption of innovation, particularly from the point of view of usage. This paper will identify some of the scientific barriers that need to be overcome in order to provide a rigorous basis for an MBSE adoption support approach.
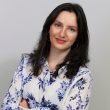
Léa Kozak
PhD student,
Université de Lorraine
The algorithm based on Kalman filtering was proposed to calculate yaw steering angles of spaceborne Synthetic Aperture Radar (SAR) systems. We establish the process equation and the observation equation by proper design. Performance analysis and computer simulations demonstrate that Kalman filtering may take advantages in both numerical precision and computational efficiency. It therefore can be applied to SAR satellites in a wide range of microwave bands (C, X, Ku) along noncircular orbits. In addition, an efficient algorithm based on simple interpolation may be employed in practice. Since the Kalman filter is linear in nature, the fast computation makes possible the implementation of accurate onboard processing.
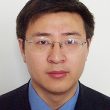
Yongfei Ding
Vice President,
Aviation Industry of China (AVIC)